CIOP training and certification program is delivered over 90 hours of classroom/online training in corporate and retail batches. The uniqueness of this program is that it addresses the modern supply chain trends without loosing the traditional aspects. This program prepares the participants for supply chain management in 2025 and beyond by infusing the learnings need in the areas of industry 4.0 such as Internet of Things (IoT), Blockchain, Artificial Intelligence (AI), Machine Learning (M/L) and Robotic Process Automation (RPA). It also deals with process improvement philosophies, methods, and tools such as Microsoft Visio. The program deals with almost 50+ supply chain analysis techniques.
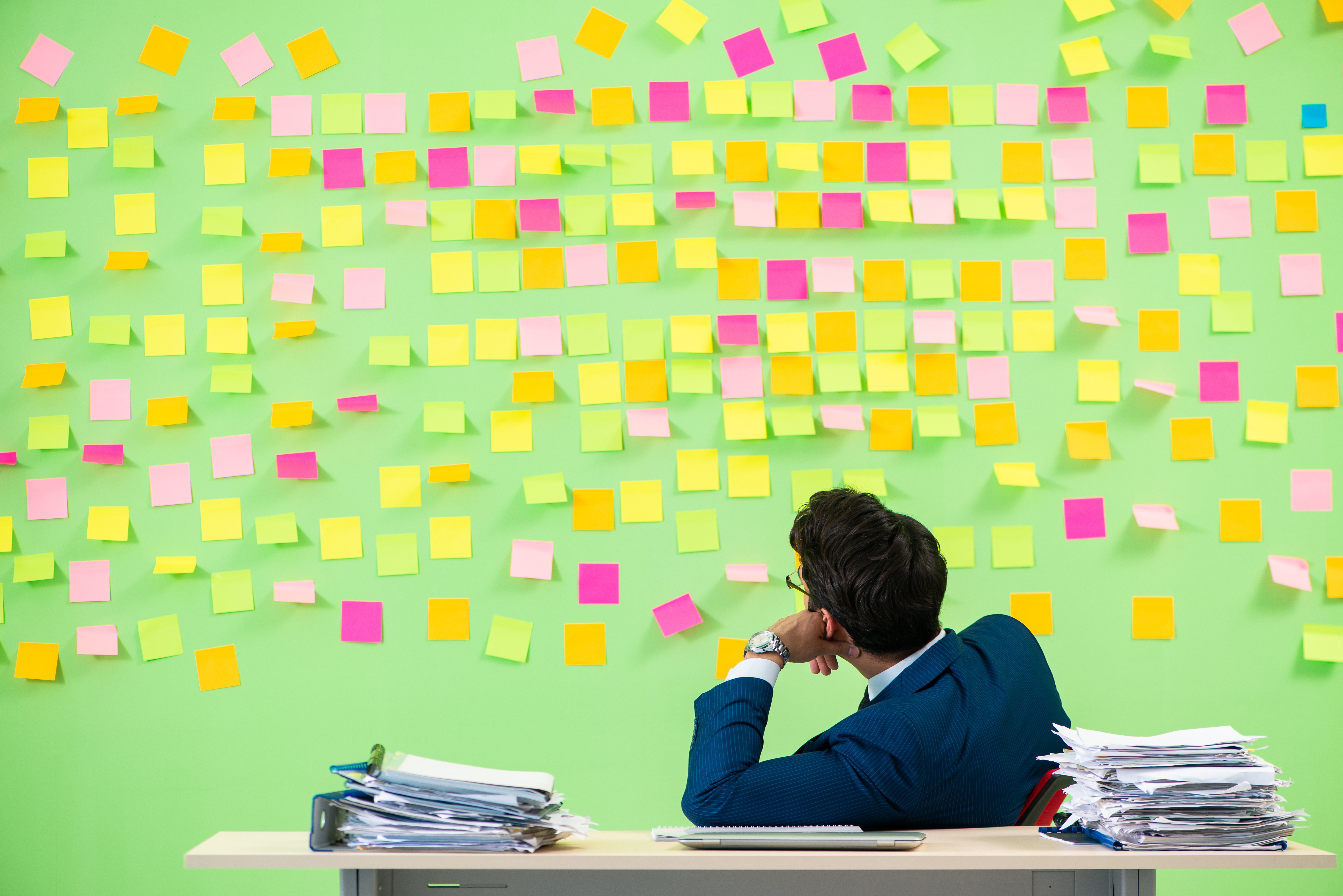
In warehouse operations, back scheduling is vital for inventory control, as well as for reducing operation costs. Back scheduling is a method for estimating scheduled operation start times and delivery dates using historical demand, available stock, and manufacturing capacity. The
schedule is calculated starting with the current date and working backwards to estimate the number of units needed, based on historical demand and available inventory levels. This method is particularly useful for shortening turnaround times, which is especially important in warehousing operations that must meet delivery targets on a short time frame. Back scheduling reduces inventory holding times by adjusting orders and shipment dates to minimize late delivery.
Back schedules (or backtracking) is an optimization strategy that helps identify and eliminate waste in an operation. The goal of back scheduling is to ensure that resources are reserved when needed the most, while avoiding unnecessary delays in critical paths. The backtracking system identifies potential problems areas by observing a particular production flow or by manually inspecting all critical paths. It then creates a scheduling template, which enables one to easily create a customized, dynamic, and accurate schedule without manual intervention. The scheduling templates are reusable across all locations, reducing manual correction of previously set production schedules.
Back scheduling methods are useful for analyzing and controlling inventory and order supply. It can also be used to schedule back order fulfillment to improve order flow and reduce lag time between orders. Other uses include determining the right order mix for critical and over-ishable commodities. Back scheduling also prevents the occurrence of too many unplanned interruptions in production. Other benefits include increasing inventory lead time, decreasing facility downtime, improving distribution management, and increasing company profitability.
Related Articles
Back Scheduling Forward Scheduling vs. Backward Scheduling in Production Planning
Forward and Backward Scheduling: Definitions, and How You Can Use Them to Compete
Forward Scheduling vs Backward Scheduling: Best for Manufacturers
Backward Production Scheduling
Backward or forward scheduling?
Certified Inventory Optimization Professional
CIOP is an end-to-end supply chain certification that contains 30 modules such as Introduction to Supply Chain Management, All About Inventory, Production Planning System, Strategic Business Planning, Sales & Operations Planning, Master Scheduling, Material Requirements Planning, Demand Management, Capacity Management, Forecasting, Production Activity Control, Procurement, Order Quantities, Independent Demand Ordering Systems, Warehouse Management, Transportation Management, Supplier Relationship Management (SRM), Customer Relationship Management (CRM), Introduction to Quality, Introduction to Packaging, Introduction to Process, Lean, Six Sigma, Total Quality Management, Theory of Constraints, Supply Chain Technologies, Supply Chain Techniques, Industry 4.0, International Standards and Supply Chain Risk, Safety and Security.
Learn More
CIOP Knowledge Series
One-Minute Supply Chain Facts
The most recent video is available here. To access the past videos in the One-Minute Supply Chain Facts Series, please click the playlist icon located on the Top-Right of the video.