CIOP is an end-to-end supply chain certification program that focuses on practical aspects in addition to the theoretical concepts. For example, a typical supply chain certification may teach what is cycle counting and how to do the ABC classification. CIOP starts with these fundamental concepts and goes on to teach the participants to develop the cycle counting policy of an organisation, 10+ criteria used in ABC classification, multi-criteria ABC classification and cycle counting best practices to increase the efficiency and effectiveness. In case of CIOP, you learn the concepts and will be ready to implement in your day-to-day job in supply chain. The pedagogy is structured such a way that all the concepts are explained with industry examples, which makes CIOP as the preferred training and certification program for supply chain within the industry.
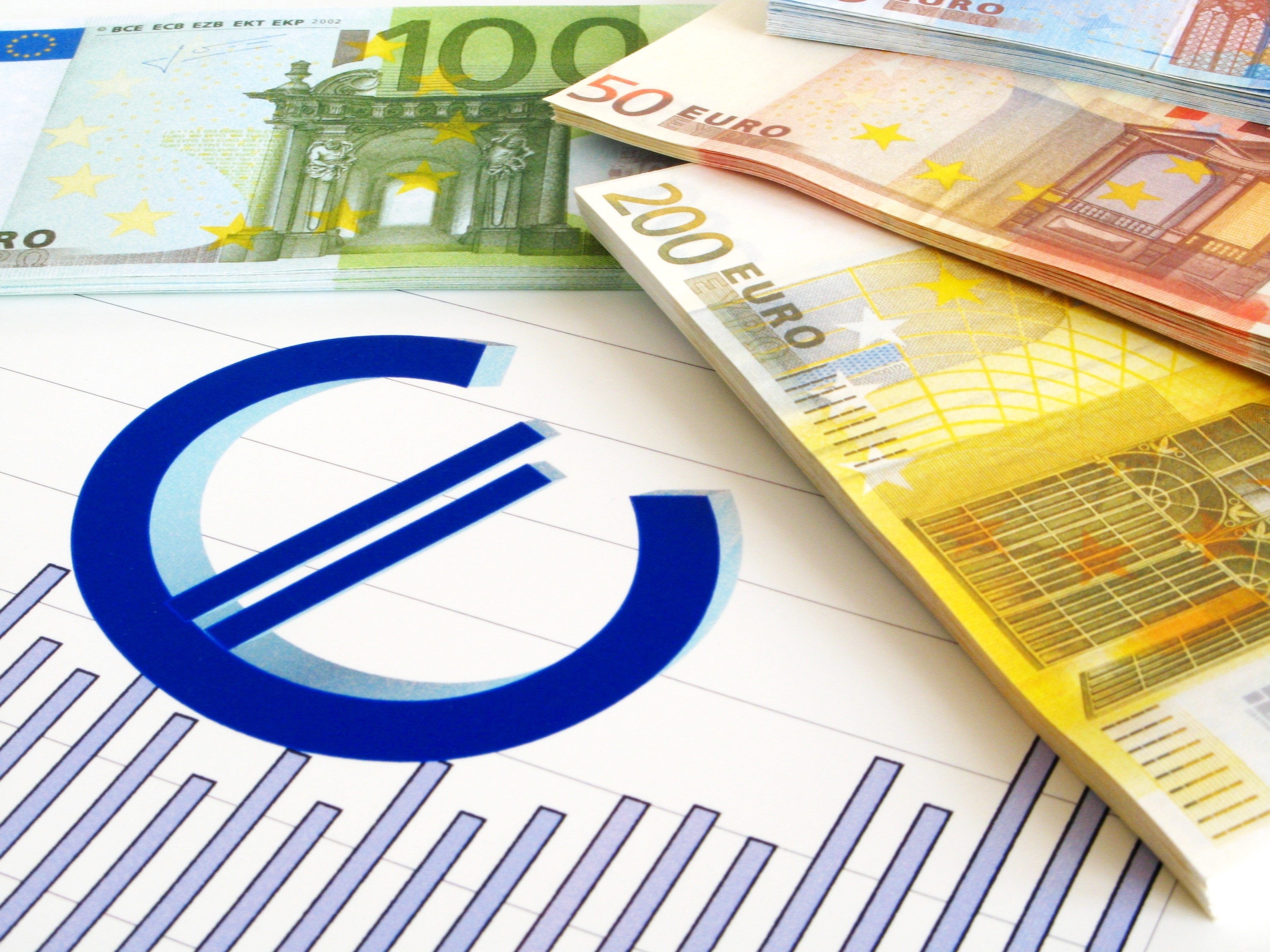
In supply chain management, the term Average Cost of Supply (ACOS) is used to represent the level of pricing for goods or services offered in any supply chain. Definition: The Average Cost is the per item cost of production
multiplied by the total value (T), which represents the total number of units required to reproduce the item. By per item cost of production, we mean that all variable and fixed costs are taken into consideration for computing the average cost. Variables such as output, quantity, and quality are included in determining the ACOS. And variables such as price, timing, and competition are not included in it.
In inventory valuation methods, the concept of Average Cost of Supply (ACOS) is used. The goal of inventory valuation is to determine the cost of goods sold to the ultimate buyer. Goods sold in a production environment are generally on-hand or nearly on hand. If there is a problem or error during the production process, the goods sold to customers are usually delayed. If consumers feel better with goods that have been sold at lower prices, they will buy again.
To calculate the ACOS, the quantity of inputs that are required for each output is needed. The quantities of inputs depend on the scale of the industry, the scale of the product, and the scale of the company. On the output side, the key terms to use are the amount of goods produced, the amount of good sold, the level of competition for each good, and the cost per units of output. Each key term is derived from one of the following sources: the sales volume of each good, the cost per units of sales, the cost per unit of gross sale, the cost of good sold in the case of an intangible good, and the price of the good in the case of a tangible good. Many companies use more than one of the key terms to arrive at the ACOS.
Certified Inventory Optimization Professional
CIOP is an end-to-end supply chain certification that contains 30 modules such as Introduction to Supply Chain Management, All About Inventory, Production Planning System, Strategic Business Planning, Sales & Operations Planning, Master Scheduling, Material Requirements Planning, Demand Management, Capacity Management, Forecasting, Production Activity Control, Procurement, Order Quantities, Independent Demand Ordering Systems, Warehouse Management, Transportation Management, Supplier Relationship Management (SRM), Customer Relationship Management (CRM), Introduction to Quality, Introduction to Packaging, Introduction to Process, Lean, Six Sigma, Total Quality Management, Theory of Constraints, Supply Chain Technologies, Supply Chain Techniques, Industry 4.0, International Standards and Supply Chain Risk, Safety and Security.
CIOP Knowledge Series
One-Minute Supply Chain Facts
The most recent video is available here. To access the past videos in the One-Minute Supply Chain Facts Series, please click the playlist icon located on the Top-Right of the video.