CIOP sessions are conducted by a pool of faculties who also offer the other international certification programs. The typical faculties are having experience between 20 to 30 years in the domains of procurement and supply chain and have a wealth of industry and teaching experience. All of them have great passion for teaching and believes in continuous learning and sharing those learnings. The faculties also go through periodic trainings titled “Faculty Development Programs” to keep them abreast with the latest developments in supply chain and teaching methodologies. Basically, all the faculties are practitioners or consultants who work for the industry and teach supply chain during their spare time or execute this as a project.
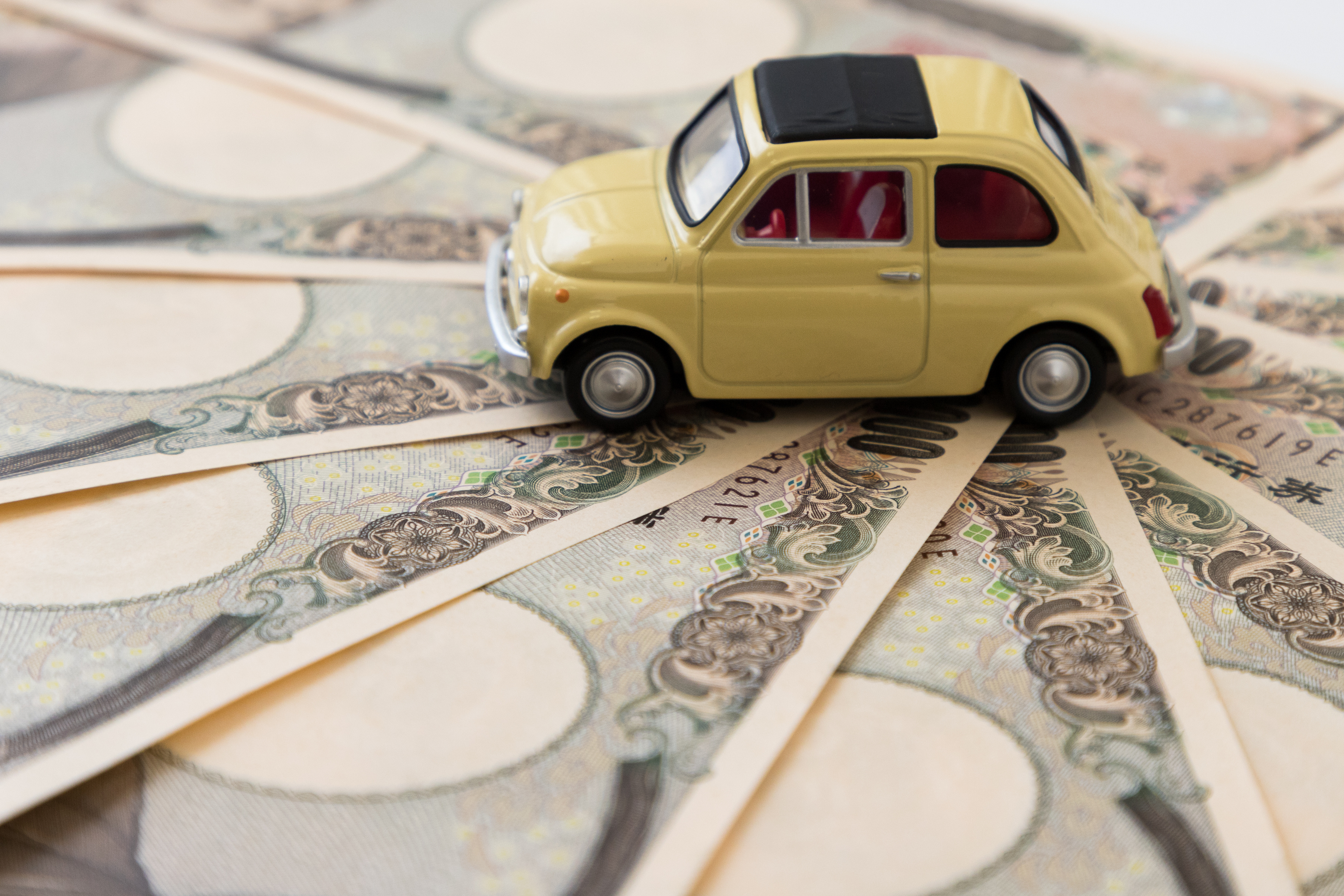
Appraisal Costs are a specific category of inventory costs. For many companies, the money that would be lost due to the sale of defective goods or services far exceeds the appraised costs.
Appraisal Costs are fees which a company pays to discover faults in its goods before delivering them to end users; they often are part of a supply chain management strategy. In supply chain management, an organization's biggest expenses are those which are not directly associated with actual goods or services.
For example, if a firm needs raw materials in order to produce a product, it will incur an inventory cost of acquiring the raw materials and then storing them until they can be used to manufacture a product. The warehousing cost then comes into play when the customer requires that particular product and requires the raw materials at a particular time. If the firm has no inventory to provide to the customer, it must then obtain the inventory (e.g., by buying products in bulk and storing them until the customer requests for the items) from another firm, which in turn must transport the items to the customer. This causes the firm to incur yet another cost: the expense of storing the inventory.
Appraisal-cost analysis is part and parcel of any quality measurement process. Quality management efforts are not always successful; sometimes firms can spend too much time focusing on process improvement rather than solving the problems that cause them inventory turnover and lack of profit. Inventory management is not just about storing finished goods; it is also about having a system in place for managing the whole process of receiving, storing and making deliveries, so that the whole life cycle of the firm's activity from starting to finish is well managed. This involves processes such as contract management, logistics management and supplier selection.
Certified Inventory Optimization Professional
CIOP is an end-to-end supply chain certification that contains 30 modules such as Introduction to Supply Chain Management, All About Inventory, Production Planning System, Strategic Business Planning, Sales & Operations Planning, Master Scheduling, Material Requirements Planning, Demand Management, Capacity Management, Forecasting, Production Activity Control, Procurement, Order Quantities, Independent Demand Ordering Systems, Warehouse Management, Transportation Management, Supplier Relationship Management (SRM), Customer Relationship Management (CRM), Introduction to Quality, Introduction to Packaging, Introduction to Process, Lean, Six Sigma, Total Quality Management, Theory of Constraints, Supply Chain Technologies, Supply Chain Techniques, Industry 4.0, International Standards and Supply Chain Risk, Safety and Security.
CIOP Knowledge Series
One-Minute Supply Chain Facts
The most recent video is available here. To access the past videos in the One-Minute Supply Chain Facts Series, please click the playlist icon located on the Top-Right of the video.