CIOP sessions are conducted by a pool of faculties who also offer the other international certification programs. The typical faculties are having experience between 20 to 30 years in the domains of procurement and supply chain and have a wealth of industry and teaching experience. All of them have great passion for teaching and believes in continuous learning and sharing those learnings. The faculties also go through periodic trainings titled “Faculty Development Programs” to keep them abreast with the latest developments in supply chain and teaching methodologies. Basically, all the faculties are practitioners or consultants who work for the industry and teach supply chain during their spare time or execute this as a project.
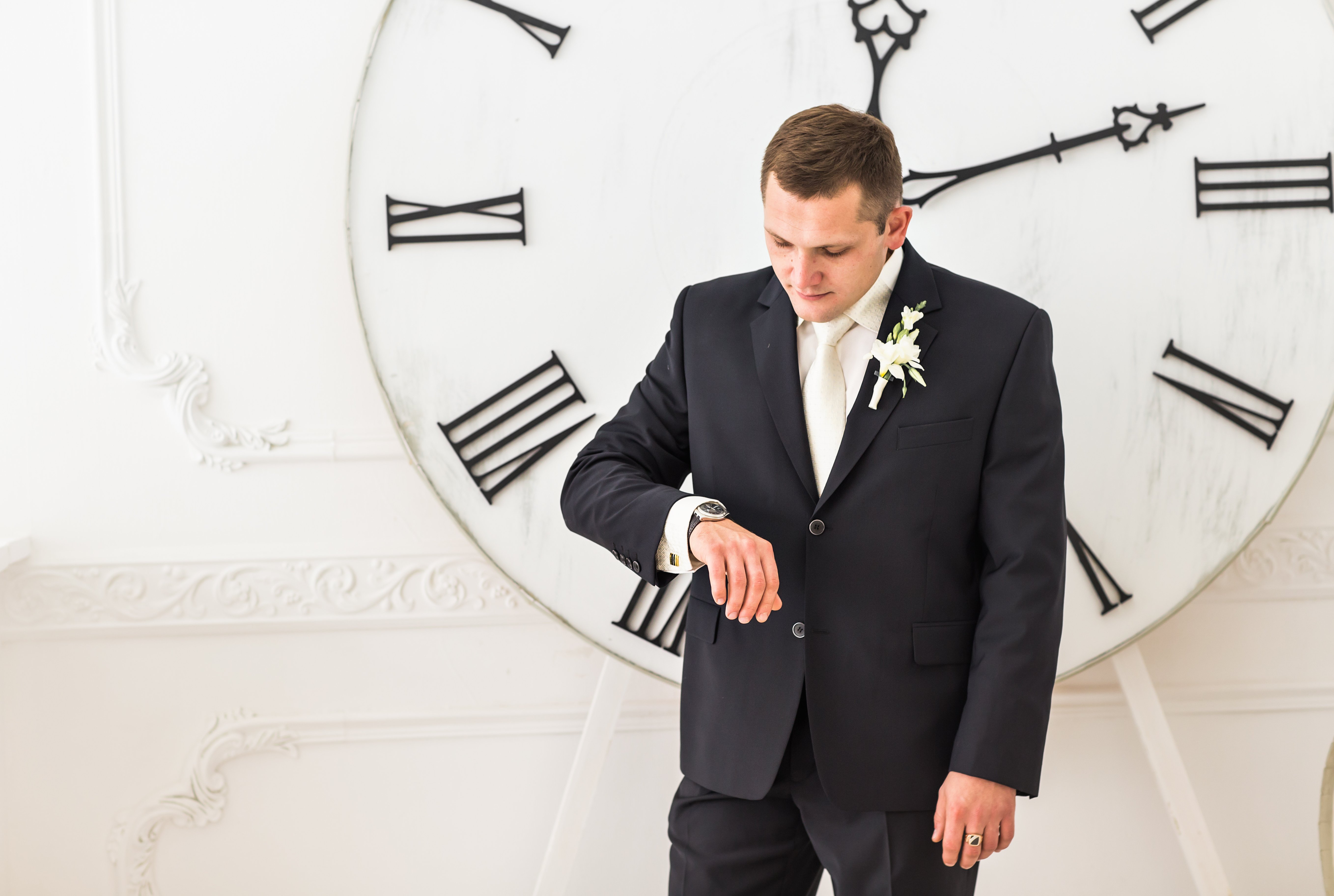
Backward scheduling is a method used in manufacturing processes when no product is on hand at the time of scheduled arrival. Forward scheduling computes the earliest possible date that the product would be available if no supply is available at the time of the scheduled delivery. The method then
does an additional check to see if the initial expected date is still valid, forming the basis for future scheduling. Forward scheduling essentially subdivides the current inventory by date. The back of the stock is only available when the product is needed.
When forward scheduling is used for manufacturing, it is often combined with other techniques such as load balancing and demand balancing. For example, in case of a service industry, the service centers usually have a series of fixed dates which are used for calculating their inventory levels. The manufacturing facility can use these same production dates to generate their own back of stock reports. In a manufacturing environment, this information can help them increase their order quantities at the right time. In addition, it allows them to anticipate any problems that may arise due to unavailability of certain raw materials, and in the case of overages, to keep production running at its optimum level.
In addition to manufacturing applications, this method is also used in finance sectors for calculating the cash flows for operations and purchases. The most common application of the backward scheduling method is in sales. A salesperson's order time is directly affected by the time he needs to collect his payment. Thus, it becomes necessary to start the payment collection process on the last working day of the month, to meet the client's payment deadlines. By performing back of stock calculations based on the latest available shipment status, the salesperson can determine whether to place an order for more or less than what is required to fulfill the entire order.
Certified Inventory Optimization Professional
CIOP is an end-to-end supply chain certification that contains 30 modules such as Introduction to Supply Chain Management, All About Inventory, Production Planning System, Strategic Business Planning, Sales & Operations Planning, Master Scheduling, Material Requirements Planning, Demand Management, Capacity Management, Forecasting, Production Activity Control, Procurement, Order Quantities, Independent Demand Ordering Systems, Warehouse Management, Transportation Management, Supplier Relationship Management (SRM), Customer Relationship Management (CRM), Introduction to Quality, Introduction to Packaging, Introduction to Process, Lean, Six Sigma, Total Quality Management, Theory of Constraints, Supply Chain Technologies, Supply Chain Techniques, Industry 4.0, International Standards and Supply Chain Risk, Safety and Security.
CIOP Knowledge Series
One-Minute Supply Chain Facts
The most recent video is available here. To access the past videos in the One-Minute Supply Chain Facts Series, please click the playlist icon located on the Top-Right of the video.