CIOP training and certification program is delivered over 90 hours of classroom/online training in corporate and retail batches. The uniqueness of this program is that it addresses the modern supply chain trends without loosing the traditional aspects. This program prepares the participants for supply chain management in 2025 and beyond by infusing the learnings need in the areas of industry 4.0 such as Internet of Things (IoT), Blockchain, Artificial Intelligence (AI), Machine Learning (M/L) and Robotic Process Automation (RPA). It also deals with process improvement philosophies, methods, and tools such as Microsoft Visio. The program deals with almost 50+ supply chain analysis techniques.
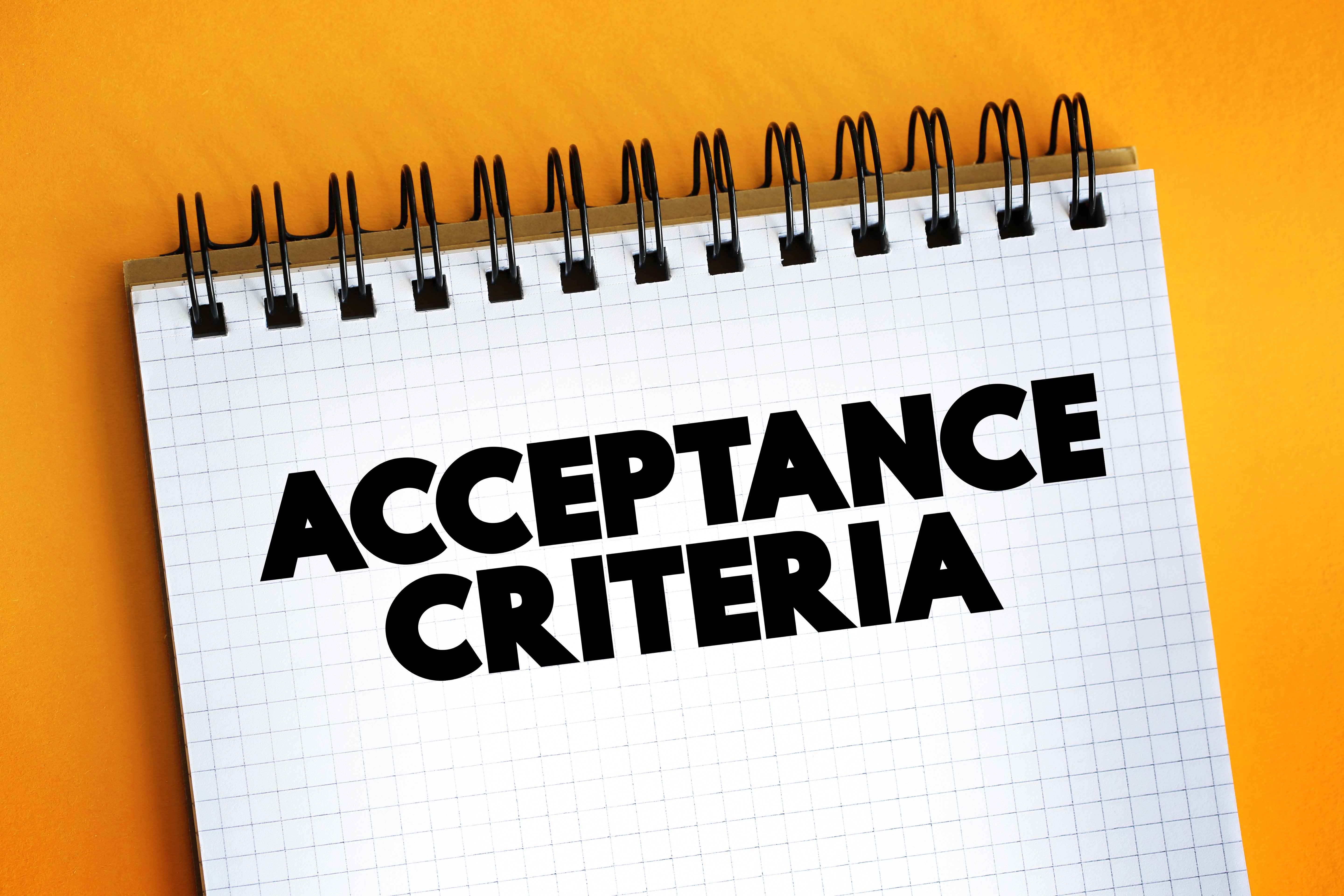
Inventory, Acceptance Criteria, and Production are three important but often overlooked components of manufacturing performance management. These three terms are often used interchangeably and many in the manufacturing supply chain don't understand the difference between the three. Each term is vital to the process of manufacturing and each impacts the way production occurs. In order for a company to successfully meet the demands of the marketplace, every piece of production equipment should be properly tested to ensure it meets production needs and that customers receive full value for their purchase.
Acceptance Criteria An inventory procedure utilized to determine whether the requirements of a proposed contract or specification are met. The inventory manager will validate material, services, and other factors that affect the production and manufacturing process to determine what products will be available. Once an inventory has been established, goods may be shipped to manufacturers or distributors, or to sales outlets. Acceptance Criteria, also referred to as PMI (PMS), is a reduction of waste of good that results from faulty or inefficient product specifications. By reducing the number and type of errors that occur throughout the manufacturing process, acceptance criteria help to ensure that quality control, service, support, and goods return with a minimum loss of financial investment.
Production Metrics The production metrics will help to establish the amount of materials, equipment, and labor necessary to manufacture a specific product. It will also include the costs of raw materials, transportation costs, and overhead such as wages and supplies. Warehousing costs, including space requirements, are included in the production metrics. These three components are essential for determining the costs of manufacturing and the final costs of receiving the finished goods from the suppliers.
Certified Inventory Optimization Professional
CIOP is an end-to-end supply chain certification that contains 30 modules such as Introduction to Supply Chain Management, All About Inventory, Production Planning System, Strategic Business Planning, Sales & Operations Planning, Master Scheduling, Material Requirements Planning, Demand Management, Capacity Management, Forecasting, Production Activity Control, Procurement, Order Quantities, Independent Demand Ordering Systems, Warehouse Management, Transportation Management, Supplier Relationship Management (SRM), Customer Relationship Management (CRM), Introduction to Quality, Introduction to Packaging, Introduction to Process, Lean, Six Sigma, Total Quality Management, Theory of Constraints, Supply Chain Technologies, Supply Chain Techniques, Industry 4.0, International Standards and Supply Chain Risk, Safety and Security.
CIOP Knowledge Series
One-Minute Supply Chain Facts
The most recent video is available here. To access the past videos in the One-Minute Supply Chain Facts Series, please click the playlist icon located on the Top-Right of the video.